Anodizing titanium is a similar process to anodizing aluminum. The titanium is used as the anode in an electrolyte bath. A charge is applied to the part and the flow of ions creates a titanium oxide layer on the surface of the part. The organized crystalline structure of the oxide layer provides corrosion protection, abrasion resistance and anti-galling properties in the titanium. It can also be useful for medical implants for its increased biocompatibility properties.
We offer titanium anodizing services compliant with AMS 2488 Type II and titanium color anodizing (sometimes referred to as Type III). Typically used in aerospace and medical applications, Type II titanium anodize produces excellent anti-corrosion and anti-galling properties. One unique property of Type II is that it does not change the overall dimensions of the part. Rather than adding a layer on top of the material, it grows the oxide layer down from the surface ensuring that tightly toleranced parts fit together after finishing exactly as they did during mock-up.
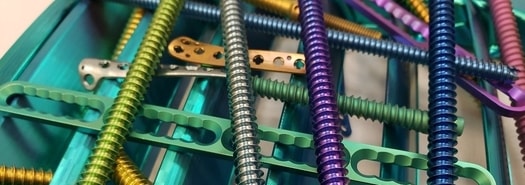
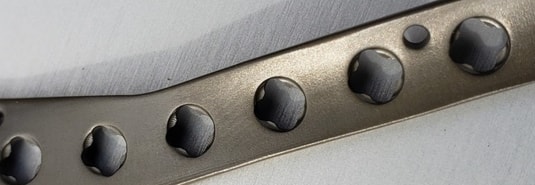
Color anodize, sometimes referred to as type III titanium anodize, creates a brilliantly colored surface finish. Unlike aluminum color anodizing, titanium color anodizing uses no dye, instead the color is determined by the light interacting with the varying thicknesses of the oxide layers. Thin layers produce colors in the tan and dark blue ranges while bright green and pink are produced with the thickest coating. Typical applications are color-coding for medical devices such as bone screws and plates as well as decorative finishes for jewelry, automotive parts, firearm parts, and outdoor equipment.